ある会社の1コマ <大手からの型受注について>
お盆を過ぎ各地でゲリラ豪雨が発生し、被害にあわれた方のお見舞い申し上げます。
名古屋オフィスのコンサルタントCが私の経験も合わせて様々情報を提供していきます。
<大手からの型受注について>
M社は、大手メーカーより生産型の受注を継続的に行っておりました。
見積の段階では、メール・FAXなどで図面を頂き金額を提出しておりました。
生産型の受注が3点決定し、CADデーターなどを入手し製作をしていきます。
工程は
CADデーター入手 → 原形型 → マスター型 → 生産型 → 検査 → 納品
と大まかな流れです。
近年はデーターを入手しての製作で以前の様な図面を読み取って原形型を製作よりはミスが少なくなりました。また、NCなどの普及により高度な加工が行えるようになりました。
但し、元データーが間違っていないという条件が付きます。
一度、大きな問題が発生しました。
メーカーから送られてきたデーターが意図していた形状になっておりませんでした。
生産型が完了し、納品検査で問題がわかり、緊急対策会議です。
日程はもうありません。
メーカーからは、生産型は3型あるので問題の1型の製品製作を最後にし、それまでに新しい型を納入してほしいとの要望がありました。
型製作メーカーは、目が点になりました。
(納期的には1週間ありません)
生産型の使用予定を聞いてみますと製品3ヶを展示用に製作し、その後は2~3週間後に量産を行うとのことでしたので、まず現状生産型の違う部分を加工し、3ヶだけ製品を製作し表面処理加工を行う。
その後、マスター型を改造し、量産用の生産型を作り直すとの提案を行いました。
提案は受け入れられ無事量産体制の構築が行えました。
・当然の事ですがデーターの確認を複数人で行う。
今回のケースでは、2名の図面検査を受け外部に提出されています。
検査の仕組みがあるのですがうまく機能していないといった欠点があります。
人を信頼するということと仕組みの上での検査は別物です。
機能する仕組み作りが重要です。
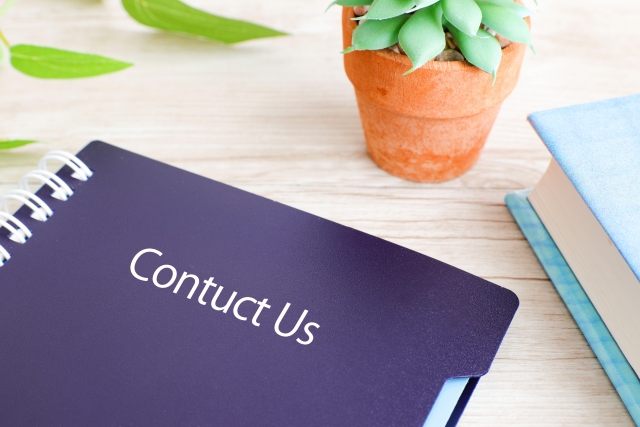
お問い合わせ
ご質問やご相談などお気軽にお問い合わせください